تست غیر مخرب NDT چیست ؟!
تست غیر مخرب NDT که مخفف کلمه انگلیسی (Non Destructive Testing ) است ، روش تست غیرمخرب ویژگی های مکانیکی و سایر ویژگی ها را بدون تخریب قطعه است ، که باعث صرفه جویی در وقت و هزینه در تست قطعه می شود.
تست های غیر مخرب انواع مختلفی دارند که در این مقاله سعی میکنیــــم مهمترین آنها را توضیح بدهیم ، از تست های غیر مخرب بصورت گسترده در بازرسی جوش ، بازرسی قطعات ریختهگری شده ، قطعات فورجینگ یا آهنگریشده ، تخمین عمر خستگی ، بررسی میزان خوردگی و …. استفــاده میشود روش هایی که در این مقاله بررسی میکنیم دذ حدود ۹۰ درصد روش های غیر مخرب را پوشش میدهد و سایر روش ها که ممکن است در صنعت از آنها استفاده شود ، کاربرد خاص دارند.
انواع روش ها تست غیر مخرب
- تست چشمی (VT)
- تست مایع نافذ(PT)
- تست مغناطیسی(MT)
- تست رادیوگرافی(RT)
- تست جریان گردابی(ET)
- تست التراسونیک(UT)
- تست اکوستیک امیشن(AME)
- تست ترمو گرافی (IR)
- تست نشتی (LT)
- تست موج هدایت شونده (GWT)
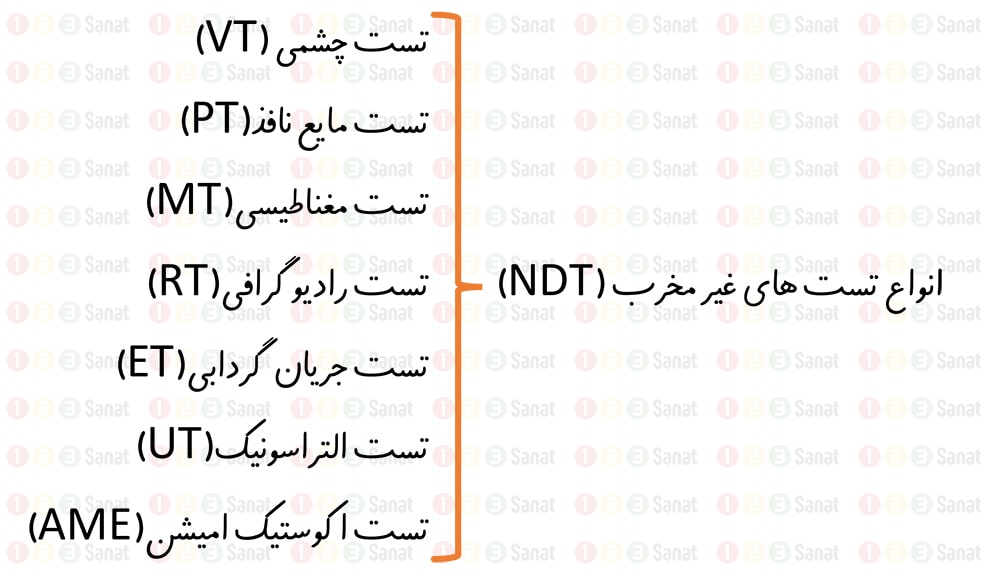
تست چشمی (VT)
تست چشمی (VT) که مخفف کلمه انگلیسی Visual Testing/Inspection است . قدیمی ترین و اساسی ترین روش آزمایش غیر مخرب است ، اما همچنین قدرت تشخیص بالایی ندارد . تست چشمی فقط عیوبی قابل تشخیص است که باعث تغییر در ظاهر قطهه شده باشند و این بزرگتــــرین محدودیت تست چشمی (VT) است .
مزایــــا و محدودیت های تست چشمی (VT)
مزایا
- ارزان قیمت
- ایمن بودن
- عدم نیاز به تجهــیـزات اضافه
محــدودیت
- قابلــیت تشخیص عیوب ظاهری
- امـــکان خطای انسانی
- نیــازمند کارشناس آموزش دیده
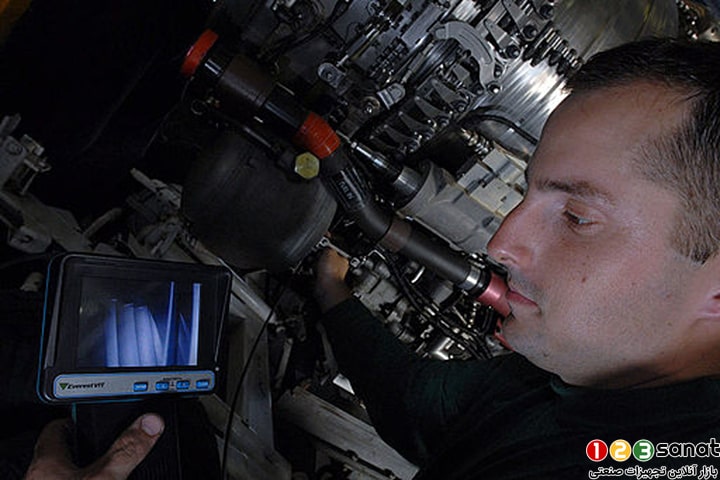
تست مایع نافذ(PT)
تست مایع نافذ(PT) که مخفف کلمه انگلیسی Penetrant Testing است . اغلب برای تشخیص نقص سطح قطعات ریخته گری ، قطعات آهنگری و جوشکاری مورد استفاده قرار می گیرد. عیوبی مانند شکستگیهای مویی و انواع ترک های سطحی با این روش قابل تشخیص است.
اساس تست مایع نافذ(PT) بر خاصیت موینگی است و این صورت است که ابتداً مایع نافذ در داخل ترک های احتمالی نفوذ میکند و سپس آشکارساز با بیرون کشیدن ، مایع نافذاز داخل منـــافذ سبب آشکــار شدن عیوب میشود و مراحل آن بشرح زیر است :
۱) تمیزکاری (Cleaning)
وجود آلودگی روی سطح قطعه کار مانع نفوذ مایع نافذ به داخل ترک و شکاف روی سطح میشود ، لذا مهم است قبل از انجام آزمایش سطح از وجود آلودگی هایی مانند چربی ، زنگ زدگی و … پاک شود
۲) آغشته کردن سطح به مایع نافذ (Applying Penetrant)
پس از تمیز نمودن و خشک شدن قطعه ، سطح را به مایع نافذ آغشته میکنیم
۳) زمان توقف (Dwell Time)
در این مرحله، مدت زمانی بین ۵ تا ۶۰ دقیقه که بستگی به دو پارامتر سیالیت مایع نافذ و حساست آزمایش دارد ، فرصت داده میشود تا مایع نافذ به داخل ترک و شکاف روی سطح نفوذ کند .
۴) پاک نمودن مایع نافذ اضافی (Penetrant Removing)
پس از گذشتن زمان توقف (Dwell Time) ، باید سطح قطعه کار از مایع نافذ اضافی تمیز بشود . این تمیز کاری بستگی به نوع مایع نافذ استفاده شده در آزمایش دارد . همانطـــــور که قبلاً اشاره شد ۳ نوع مایع نافذ ماده نافذ قابل شستشو با آب ( Water Washable Penetrant) و ماده نافذ قابل استفاده با امولسیون ( Post-Emulsifiable Penetrant ) و ماده نافذ با حلال مخصوص ( Solvent- Removable Penetrant ) وجود دارد ، که با توجه به نوع آن باید تمیز کننده مخصوص خودشان مورد استفاده قرار بگیرد .
۵) خشک کردن سطح (Drying)
اگر چه خشک نمودن سطح قبل از آغشته کردن سطح به مایع نافذ (مرحله ۲) هم می بایست انجام شود امــــــا خشک کردن سطح قبل از آغشته شدن سطح با مایع آشکارساز یا Developer اهمیت بیشتری دارد ، چرا که وجود رطوبت روی سطح میتواند بر روی آزمایش تاثیر بگذارد .
۶) آغشته کردن سطح با مایع آشکارساز (Appling Developer)
در آخرین گام انجام تست با مایع نافذ با آغشته کردن سطح با مایع آشکارساز ، سبب میشویم تا عیوب موجود در سطح قطعه کار خودشان را نشان بدهد .
۷) مشاهده نتایج
پس از مدت زمان کوتاهی بتدریج مایع نافذ گیر افتاده درون ترک ها و شکاف های سطح جذب مایع آشکارساز یا Developer شده و تصویر ترک به رنگ قرمـز روی قطعه دیده خواهد شد .
۸) پاک سازی نهائی ( Final Cleaning )
پس از رؤیت سطح قطعه و نتیجه گیری از انجام آزمایش و ثبت گزارش باید سطح قطعه از وجود اثار انجام آزمایش پاک شود .
مزایــــا و محدودیت های تست مایع نافذ(PT)
مزایا
- ارزان قیمت
- سریع بودن
- عدم نیاز به آموزش زیاد
محــدودیت
- قابلــیت تشخیص عیوب سطحی
- امـــکان خطای شناسایی در هنگام استفاده روی سطوح خشن
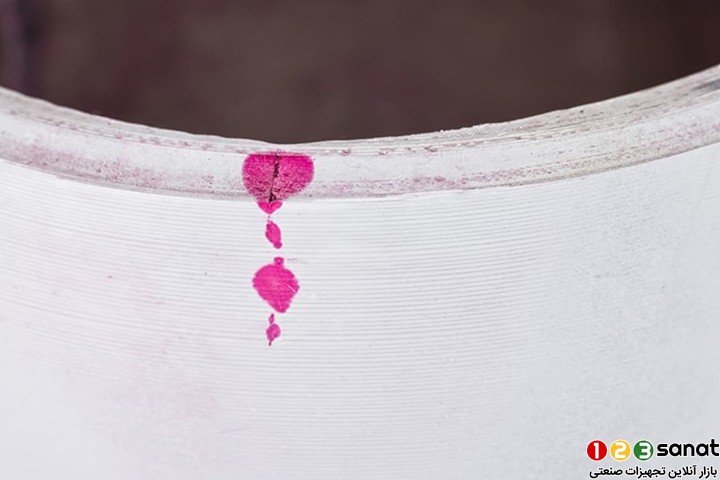
تست مغناطیسی MT
تست مغناطیسیMT که مخفف کلمه انگلیسی ( Magnetic Test ) است و گاهی اوقات با نام بازرسی ذرات مغناطیسی MPI (Magnetic Particle Inspection) شنــاخته میشود . تست غیر مخرب MT یک تست مناسب برای تشخیص نقص سطح و زیرسطحی در مکان های دور از دسترس است ، و اساس آن بر مفهوم نشت شار مغناطیسی است.
بازرسی ذرات مغناطیسی معمولاً در بیرون از منزل و در مکانهای دورافتاده برای استفاده می شود. این مبتنی بر مفهوم نشت شار مغناطیسی (Magnetic Flux Leakage) است. نشت شار مغناطیسی زمانی به وجود میآید که در نتیجه وجود ترک در داخل قطعه قطب اضافی N و S به وجود بیـــاید .
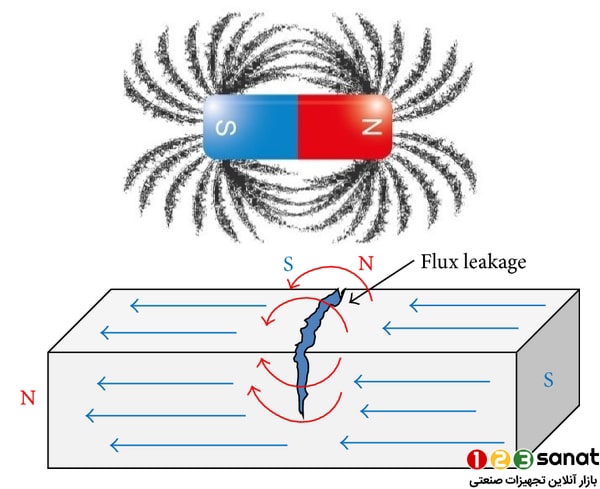
در بازرسی ذرات مغناطیسیMT، قطعه به صورت مستقیم یا غیرمستقیم آهنربا می شود. در آهنربا شدن قطعه بصورت مستقیم جریان برق مستقیم از داخل قطعه عبور داده میشود که سبب به وجود آمدن و یک میدان مغناطیسی در ماده میشود . در آهنربا شدن قطعه بصورت غیرمستقیم میدان مغناطیسی توسط یک آهنربای دیگر در داخل قطعه تست القا میشود .
از آنجا که ذرات آهن در امتداد خطوط میدان مغناطیسی متمرکز می شوند ، وقتی به قسمتی از قطعه که ترک خورده است میرسند چون در آنجا قطب اضافی N و S وجود دارد ، تجمع میکنند و با همین مکانیزیم بازرس میتواند از وجود ترک در قطعه مطلع شود .
مزایــــا و محدودیت های تست ذرات مغناطیسی MT
مزایا
- قیمت منــاسب
- ساده و سریع بودن
- عدم نیاز به تمیزکاری قبلی قطعه
محــدودیت
- قابلــیت استفاده فقط برای مواد فرومغناطیس
- غیرقابل استفاده برای قطعاتی که دارای پوشش ضخیم هستند
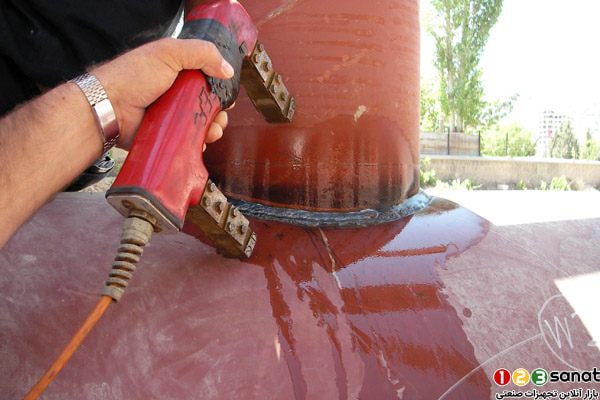
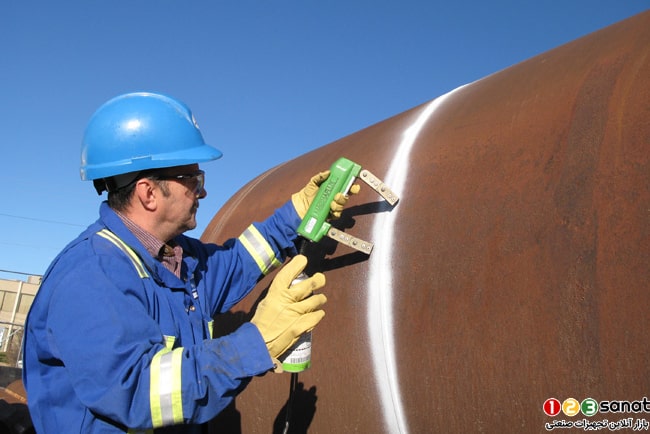
تست رادیوگرافی RT
تست رادیوگرافی RT که مخفف کلمه انگلیسی (Radiographic Test) است . برای بازرسی اجزای مونتاژ شده و یافتن نقص در سازه های پیچیده استفاده می شود. در تست رادیوگرافی RT از اشعه الکترومغناطیسی با طول موج کوتاه به شکل فوتون های پر انرژی برای نفوذ در مواد و بازرسی عیوب سطحی و زیر سطحی استــفاده میشود .
اساس بازرسی رادیوگرافی RT بر پایه اختلاف جذب انرژی تابش شده در داخل جسم است در این روش برای نفوذ اشعه به داخل جسم از پرتوهایی با انرژی بالا مانند پرتو ایکس و گاما استفاده میشود . با قرار دادن فیلم در زیر قطعه اشعه های فرستاده شده پس از عبور از داخل جسم اثر خودشان را روی فیلم باقی می گذارند و بازرس مربوطه با بازرسی این فیلم ها میتواند به عیوب احتمالی موجود در قطعه مانند تخلخل ، حبس ناخالصی و ترک و …. پی ببرد .
مزایــــا و محدودیت های تست رادیوگرافی RT
مزایا
- نیاز به آماده سازی سطح قطعه ندارد
- قابلیت تشخیص عیوب سطحی و زیر سطحی را دارد
- به عیوبی مانند خوردگی و تغییر چگالی مناطق مختلف قطعه حساس است
محــدودیت
- بعلت تششعات ، نیاز به تدابیر بیشتر برای حفظت و ایمنی کار با دستگاه است
- نیاز به دسترسی به دو طرف قطعه است
- برای تشخیص عمق عیب نیاز به عکس برداری از قطعه در زوایای مختلف است
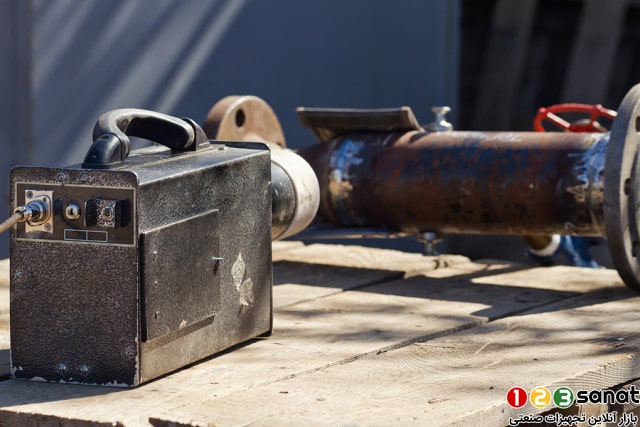
تست جریان گردابی ET
تست جریان گردابی یا تست ادی کارنت ET که مخفف کلمه انگلیسی (Eddy Current Test) است ، تست جریان گردابی برای تشخیص نقص سطح و زیرسطحی در قطعات رسانا مورد استفاده قرار میگیرد . و براساس القای الکترومغناطیسی با گذارندن جریان الکتریسیـــته متناوب از سیم پیچ است . و وجود عیب یا ناپیوستگی در ماده سبب ایجاد اختلال در جریان گردابی می شود. بنابراین کاهش جریان گردابی نشانگر وجود نقص در ماده است. نظارت بر تغییر جریان ، محل وجود عیب را نشان می دهد.
مزایــــا و محدودیت های تست جریان گردابی ET
مزایا
- حساسیت بالا
- عدم نیاز به آماده سازی سطح مانند زدودن چربی و لایه رنگ البتـــه اگر نازک باشد
- قابلیت ثبت نتایج
محــدودیت
- سرعت پایین
- قابل استفاده در مواد رسانا
- فقط قابلیت تشخیص عیوب نزدیک به سطح را دارد
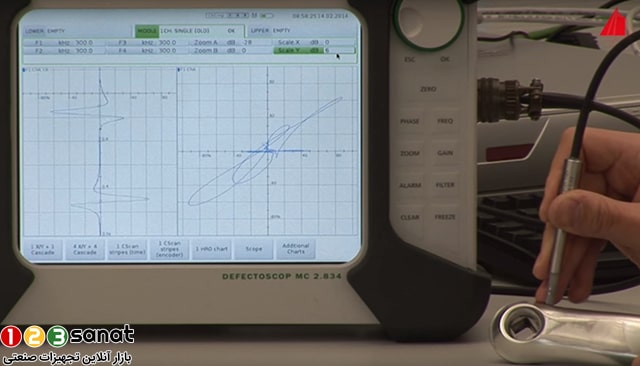
تست التراسونیک UT
تست التراسونیک یا تست UT که مخفف کلمه انگلیسی (Ultrasonic Test) است ، تست التراسونیک قابلیت تشخیص تقریباً تمام عیوب سطحی و زیر سطحی را دارد بشرط اینکه سطح قطعه صاف باشد . در تست التراسونیک از مبدل متصل به دستگاه تشخیصی برای ارسال امواج صوتی به داخل ماده استفاده می شود . و اغلب نیاز به استفاده از یک کوپلت (مانند روغن یا آب) برای اتصال مبدل و جسم دارد ، که باعث افزایش دقت در نتایج می شود.
دو روش برای دریافت سیگنال وجود دارد. روش اول Reflection یا تأمل است ، که مبدل هم سیگنــال را ارسال میکند و هم دریافت میکند و روش دوم میرایی یا Attenuation است که یک مبدل سیگنــال را ارسال میکند و یک مبدل دیگر آن را دریافت میکند و هر گونه تغیر در سیگنال نشان دهده وجود عیب در داخل قطعه است .
مزایــــا و محدودیت های تست التراسونیک UT
مزایا
- فقط دسترسی به یک طرف قطعه نیاز است
- حساسیت بالا
- قابل حمل
- سرعت بالا در نمایش نتایج تست
محــدودیت
- نیاز به کارشناس آموزش دیده
- حساس به زبر بودن سطح
- نیاز به استفاده از یک کوپلت
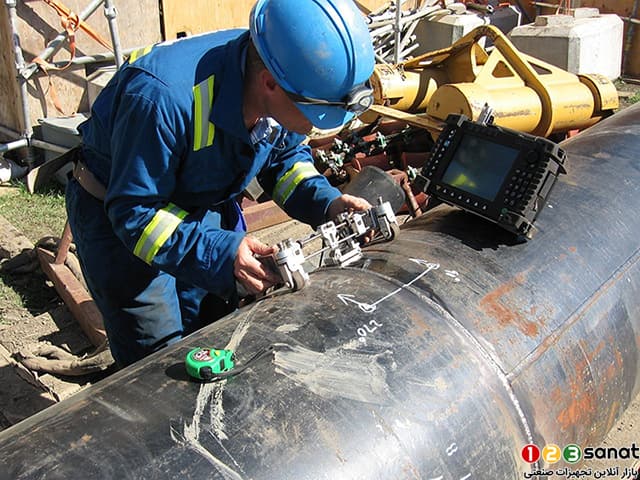
تست آکوستیک امیشن (Acoustic Emission (AE
آکوستیک امیشن یا نشر آوایی (AE) که مخفف کلمه انگلیسی Acoustic Emission است یک روش تست غیر مخرب NDT است که در آن با استفاده از سینگنال آکوستیک فرکانس بالا (در محدوده ۱۰KHZ تا ۱۰۰KHZ گاهاً این فرکانس میتواند تا ۱MHZ باشد) است . این سیگنـال که از درون اجسام و قطعات فرستاده میشود و با تحلیل سیگنال های خروجی میتوانیم میتوانیم عیوب را مشخص کنیم .
عمده کاربرد آکوستیک امیشن در موارد زیر است :
- تشخیص اصطحکاک
- تشخیص اصطحکاک و وجود سایش در بیرینگ (بلبرینگ،رولبرینگ،یاتاقان) در اثر تمام شدن گریس یا روانکار
- تشخیص ضربه در مکانیزم های دوار که بعلت لقی بیش از حد ایجاد ضربه میکند
- تشخیص تربولانس در مخازن تحت فشار که وجود نشتی بیش از حد سبب ایجاد جریان توربلانت (turbulent) میشود .
- تشخیص عیوب در قطعات تولید شده
- تشخیص عیوب در جوش
- تخمین عمر سازه
مزایــــا و محدودیت های آکوستیک امیشن یا نشر آوایی (AE)
مزایا
- قادر به تشخیص عیوب بسیار ریز در محدوده ۱µm است
- بازرسی با این روش سرعت بالایی دارد و در نتیجه راندمان کار بسیار بالا است .
- این روش نسبت به هندسه قطعه دارای حساسیت کمتــــری است .
- این روش در مقایسه با سایر روش های متداول تست غیر مخربNDT بعلت کارایی بیشتر ارزش سرمایه گذاری بالایی دارد
محــدودیت
- در این روش عیوب ایستــــا ، عیوبی که نه رشد میکنند و نه حرکت قابل شنـــاسایی نیستند البتــــه این محدودیت با اعمال تنش خارجی تا حدودی برطرف شده است .
- معیـــاری برای ارزیابی نتایج حاصل از تست نشرآوایی وجود ندارد و تحلیل نتـــایج کاملاً بستگی به دانش و تجربه کارشناس مربوطه دارد .
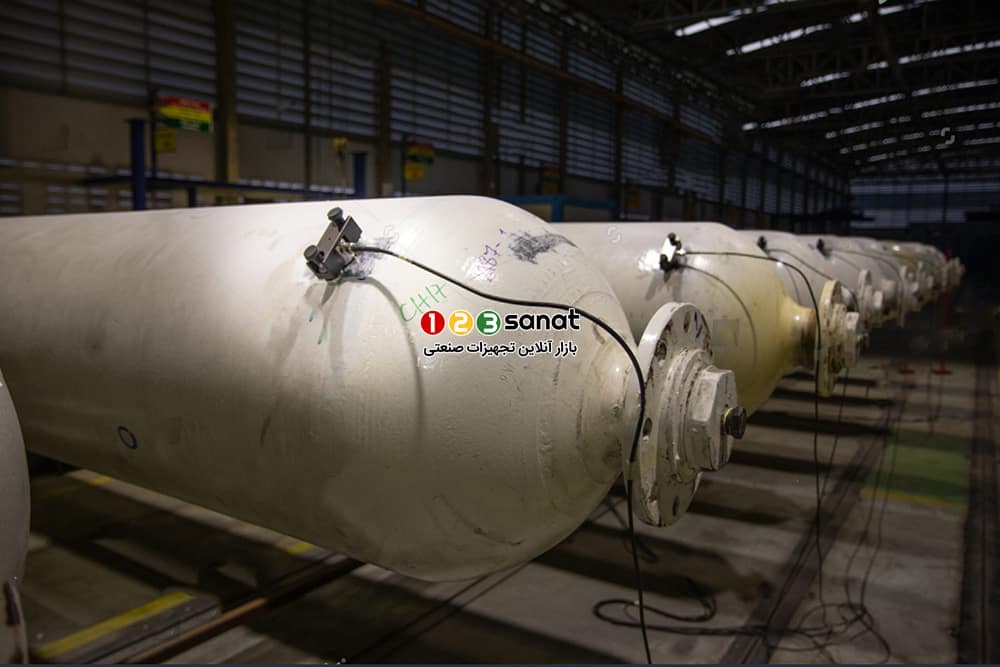
تست ترموگرافی
تست ترموگرافی برای برای یافتن ترک ها،حفره ها و سایر نقص ها در لوله ها، قطعات جوشکاری شده و سایر قطعات فلزی یا پلاستیکی استفاده می شود.
اساس تست حرارتی بر تابش اجسام است ، بطور کلی هر جسم از خود اشعه تابش ساطع می کند و هرچه یک جسم انرژی بیشتری داشته باشد ، اشعه بیشتری از خود ساطع می کند. در تست ترموگرافی از دوربین های مادون قرمز برای دیدن تابش طیف مادون قرمز و ایجاد تصویری از الگوهای حرارتی در سطح یک جسم استفاده می کند.
برای تست ترموگرافی دو رویکرد وجود دارد:
منفعل یا Passive: در این روش دمای سطح قطعه اندازه گیری میشود ، و دمای نقاط مختلف جسم با نقاط کناری مقایسه میشود و نتایج نمایش داده میشوند .
فعال یا Active: در این روش تغییر دمای نقاط سطح جسم پس از اعمال منبع حرارتی مورد بررسی قرار میگیرد .
مزایــــا و محدودیت های تست ترموگرافی
مزایا
- میتواند قبل از خرابی کامل قطعه از وجود عیب در آن ما را مطلع کند
- سریع و ایمن است
- نیاز به تماس با سطح قطعه ندارد
-
محدودیت
- فقط عیوب سطحی را نمایان میکند
- نیاز به کارشناس با تجربه
- نتایج دقت زیادی ندارند
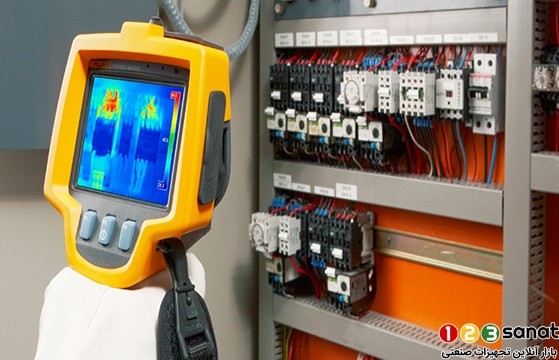
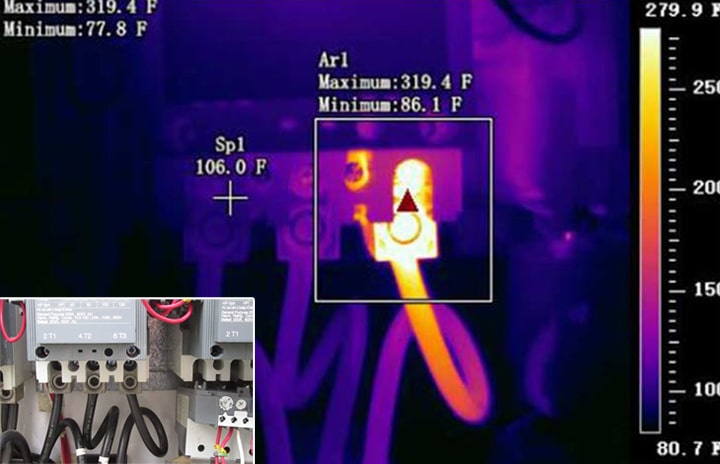
تست نشتی
تست نشتی یا LT که مخفف کلمه انگلیسی Leak Testing است ، برای تشخیص ترک یا نشتی در لوله های انتقال سیال مورد استفاده قرار میگیرد . برای ایجاد نشتی در ابتدا نیاز به اختلاف فشار در بیرون و داخل لوله داریم که سیال تمایل دارد از محل با فشار بیشتر به سمت فشار کمتر حرکت کند .
روش های مختلفی برای تست نشتی استفاده می شود ، از جمله:
۱) روش افت فشار: در روش افت فشار یا Pressure Decay ، مخزن با یک فشار مشخص پر میشود و از منبع جدا میشود و بعد گذشت زمان فشار هوا در آن مورد بررسی قرار می گیرد و میزان نشت بر اساس تغییر فشار در طول زمان محاسبه می شود.
۲) روش جریان هوای فشرده : در روش جریان هوای فشرده یا Mass Airflow ، مخزن به منبع فشار متصل میشود و فشار مخزن ، به اندازه فشار بیرون مخزن ، ثابت نگه داشته میشود و در این حالت سرعت نشت مستقیماً به عنوان سرعت جریان ورودی هوا اندازه گیری می شود.
۳) روش مشاهده : روش مشاهده یا Observation ، قطعه مورد نظر در مخزن آب فرو می رود و هر حبابی که شکل می گیرد ، محل نشت را آشکار می کند.
۴) روش ردیاب گاز (هلیوم) : روش ردیاب گاز (هلیوم) یا Gas Tracer ، مخزن آب بندی شده در یک محفظه کاملاً ایزوله قرار داده میشود و با استفاده از پمپ خلاء ، داخل مخزن و بیرون آن خلاء نسبی ایجاد میشود و سپس محفظه یا داخل مخزن (یکی از آنها) توسط گاز هلیوم پر میشود ، و با توجه به مقدار گاز از دست رفته در حجم میتوان از وجود نشتی داخل مخزن مطلع شد .
مزایــــا و محدودیت های تست نشتی
مزایا
- برخی از روش های فوق که گفته شد ارزان قیمت هستند
- ایمن است
محدودیت
- نتیجه ارزیابی کاملاً بستگی به بازرس مربوطه دارد
- نیازمند بازرسی از نزدیک است
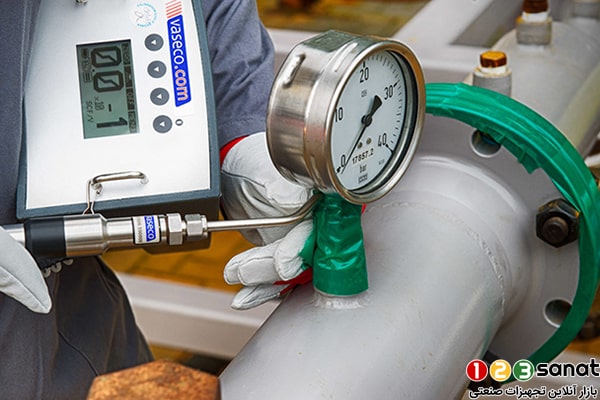
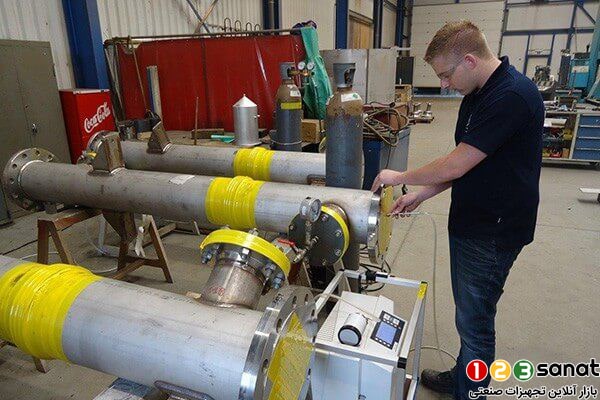
تست موج هدایت شده
تست موج هدایت شده یا GWT که مخفف کلمه انگلیسی Guided Wave Testing است ، یک روش برای بازرسی خطوط لوله و همچنین ریل های های قطار و سازه های و شفت های طویل است که با استفاده از قرار دادن دستگاه در یک مکان واحد تا ۱۰۰ متر را میتوان بازرسی کرد .
اگرچه تست موج هدایت شده یا GWT به عنوان آزمایش اولتراسونیک با برد طولانی شناخته می شود ، اما این دو روش اساساً متفاوت هستند. GWT از فرکانس پایین تر (۱۰-۱۰۰kHz) استفاده می کند و امواج متقارن محوری به صورت افقی در هر دو جهت در قطعه پخش میشوند .
در تست موج هدایت شده از پالس اکو استفاده میشود ، به این معنی که موج هم توسط ترسدیوسر تولید میشود و هم توسط آن دریافت میشود و سیگنالهای منعکس شده در صورت وجود عیب در سازه ، دریافت شان با تاخیر و تعجیل زمان همراه بوده که بازرس را از وجود و محل آن آگاه میکند .
مزایــــا و محدودیت های تست موج هدایت شونده
مزایا
- کشف عیوب سطحی و زیر سطحی موجود در قطعه
- اطلاعات تست کاملاً ضبط میشوند
- سریع است
- قابل حمل است
محدودیت
- زانویی و خمش در طول مسیر قطعه تست را دچار خطا میکند
- نیازمند کارشناس با تجربه هستیم
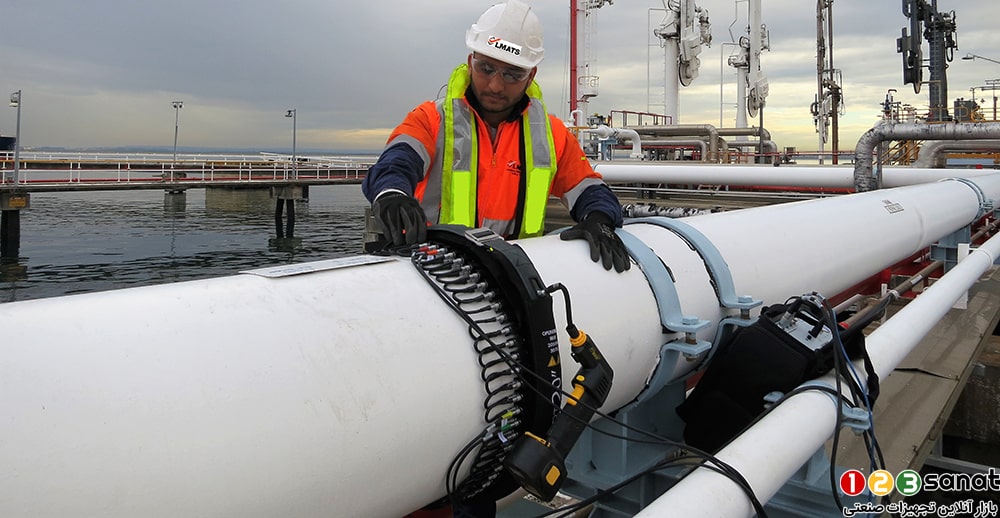